Key Components for Flow Control: Check Valve and Strainer
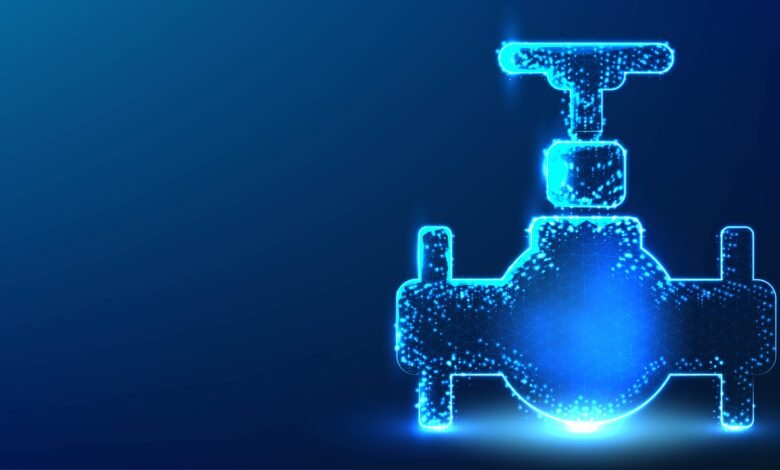
Check valves and strainers are two crucial elements in fluid systems. Both play vital roles but in different ways. Knowing their roles will help you make the right choice for your system’s needs.
Check Valves and Strainers: Saves Systems, Enhances Performance
Check valves and strainers are vital in every industrial pipe system to ensure smooth operation. These devices safeguard equipment from damage and boost system performance. Whether stopping backflow using a wafer check valve or removing debris using a custom-fabricated strainer, both have different but complementary functions.
What is a Check Valve?
A check valve permits flow in one direction only. It prevents backflow by automatically ensuring that fluid flows in the right direction. A check protects many pieces of equipment, including compressors and pumps, from damage.
Role of Check Valves
The key function of check valves is to stop the backflow of gas or liquid. Backflows mostly damage machinery, create contamination and disrupt operations. By ensuring the flow is one-way, check valves safeguard machines and pumps from the negative consequences that could occur due to reverse pressure.
Applications that experience fluctuating high pressures, such as wastewater or pipeline systems, need check valves to ensure system integrity and effectiveness.
Type of Check Valves
There are different check valves suitable for different purposes. Every type of check valve meets specific pressure, flow, and system requirements. A few of the most popular types are:
- Swing Check Valves: They feature an open disc that can swing open and close to control flow. They are great for large systems with high flow rates.
- Wafer Check Valves: These valves are lightweight and simple to install. However, they protect smaller areas that require less flow.
- Ball Check Valves: They employ balls to stop reverse flow. They are typically useful in systems with low pressure.
- Lift Check Valves: These use an engine or disc that lifts to allow flow. They automatically shut off when there is backflow. They can be useful for systems with more significant pressures.
What is a Strainer?
A strainer is a filtering device that eliminates debris, dirt, dust, and other harmful substances from gases and liquids. These particles can damage delicate devices like valves and pumps. Strainers are often located at the most critical points of the system to ensure smooth operation and avoid obstructions.
Role of Strainers
Strainers safeguard the most critical components by removing particles that could cause blockage or damage to the equipment. They are also crucial for maintaining the efficiency and longevity of valves, pumps, and pipelines.
For instance, in knife gate valves, strainers block debris from getting inside the valve, ensuring efficient functioning.
Types of Strainers
Strainers come in various types, including:
- Y Strainers: These Y-shaped strainers remove dust and debris from gases and liquids. Y strainer manufacturers design them to remove fine particles from pipelines.
- T Strainers: These T-shaped strainers are commonly useful for larger-scale systems to manage more significant amounts of particles.
- Basket Strainers: These custom-fabricated strainers accommodate large amounts of waste and are useful for high-capacity filtration.
- Custom Fabricated Strainers: These are designed specifically for specific applications where standard strainers could be more helpful. Their design is based on the system’s size and needs.
The Difference Between Check Valves and Strainers
Check valves and strainers are essential parts of fluid systems. However, they are used for distinct reasons that ensure the safety and efficiency of certain systems.
Functionality:
- Check valves stop the reverse flow of fluids. By allowing the flow in only one direction, check valves prevent backflow, which could damage equipment or disrupt the system’s functionality.
- Strainers function as filters. They eliminate dirt, debris, and other particles from the fluid. They protect equipment, like valves, pumps, and pipes, from the damage caused by pollutants.
Operation
- Check valves operate automatically. They rely on fluid to close and open. When the flow of fluid is in the correct direction, the valve will open. If the flow is reversed, the valve shuts down to stop backflow.
- Strainers employ perforated or mesh screens to collect debris as fluid moves through. The mesh size determines the dimensions of the particles removed from the fluid.
Purpose
- Check valves maintain the correct flow direction within the system. However, they prevent backflow, which could cause system malfunction or contamination.
- Strainers protect delicate equipment from damage by trapping harmful substances before they cause wear or blockages.
Maintenance
- Check Valves usually require little maintenance. However, they require regular checks for wear, particularly on the surfaces that seal them or internal components that guarantee that they are operating properly.
- Strainers require frequent cleaning to eliminate debris. If cleaned, strainers may maintain the system’s effectiveness and prevent damage.
Check valves and strainers serve different purposes but play complementary roles in the fluid system. Strainers remove contaminants and check valves to regulate the direction of flow. Both require regular maintenance to operate correctly and guarantee the durability of the whole system.
Conclusion
Check valves and strainers are crucial to ensure the proper operation of industrial pipelines. Check valves prevent backflow, whereas strainers clean out harmful particles. Different kinds, such as swing check valves or Y Strainers, are made to meet specific system requirements. Through their interaction, they improve the system’s performance, safeguard valuable equipment, and guarantee long-term effectiveness. For certain applications, a custom-fabricated strainer and check valve with a specific design, like knife gate valves, can provide customized solutions that meet specific operating requirements.
Understanding the function of each component can help you make informed choices about selecting and maintaining these essential system components.